Entwicklung
SHW ist einer der Innovationsführer für Öl-, Kraftstoff- und Wasserpumpen und für Komponenten und Systeme in konventionellen, hybriden und elektrischen Antriebssträngen und Technologieführer im Bereich Bremsscheiben.
PLUS SHW-POWER
Mit zukunftsweisenden Kernkompetenzen Internationalisierung vorantreiben & Innovationsführerschaft ausbauen.
Unsere Vision ist, führender Systemlieferant aller namhaften Fahrzeughersteller zu werden – jede Fahrzeugplattform soll mit dem Plus der SHW-Power ausgestattet sein, sprich eines unserer Systeme oder Komponenten enthalten. Unsere Produkte tragen zur Reduktion des Kraftstoffverbrauchs und zur Elektrifizierung des Antriebstrangs bei Automobilen und Nutzfahrzeugen bei. Die SHW der Zukunft wird effizienter, internationaler und noch innovativer sein.
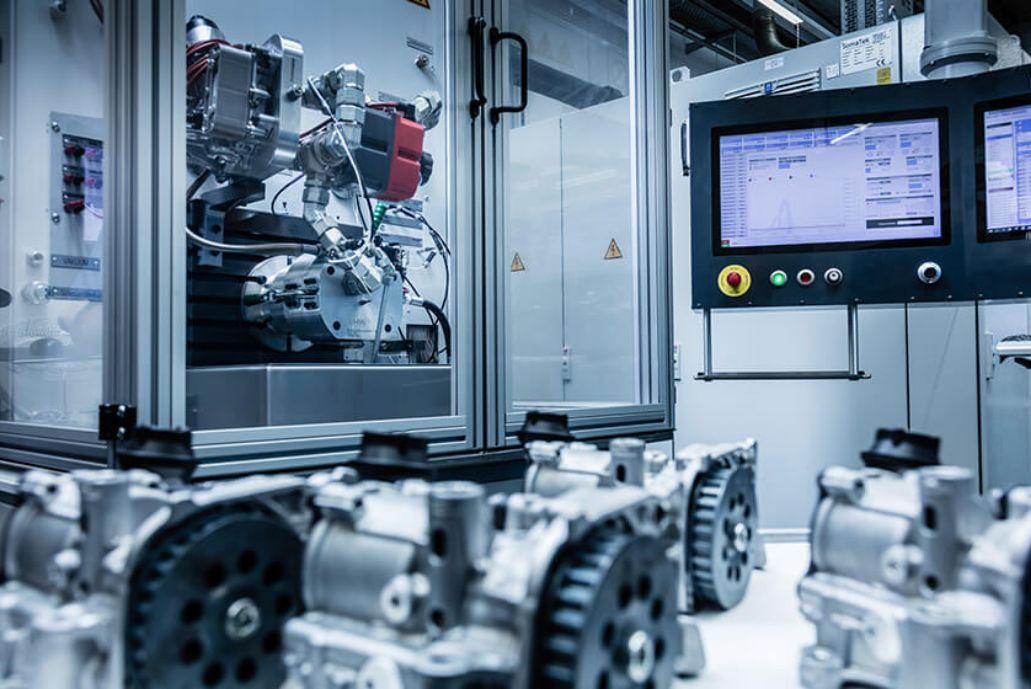
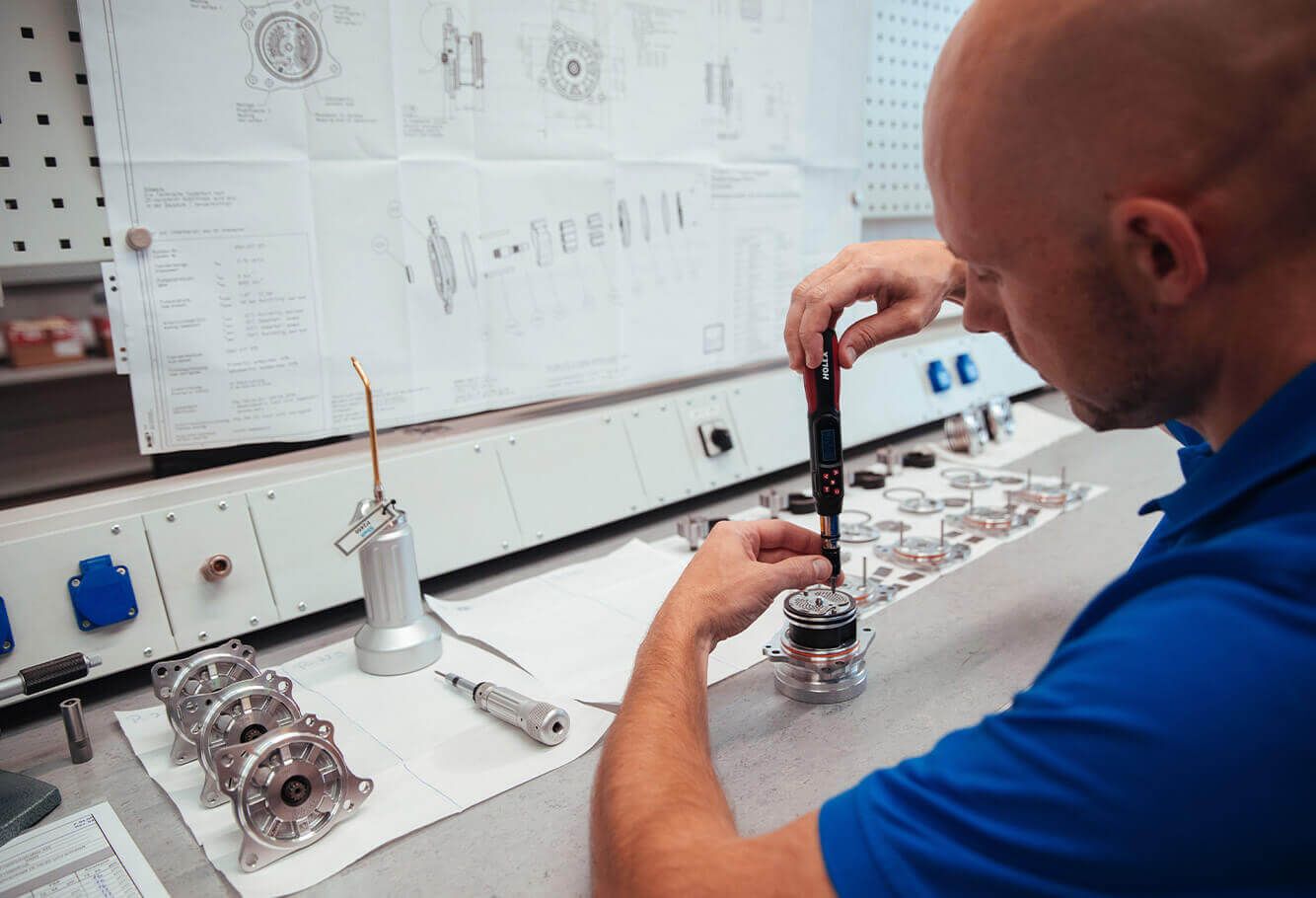
Berechnungs- und Simulationsmethoden
Vielfältige Berechnungs- und Simulationsmethoden, ein eigener Musterbau und ein umfangreiches Prüffeld zur Funktions- und Umwelterprobung von Komponenten und Systemen versetzen uns in die Lage, alle für unsere Produkte relevanten Fahrsituationen detailgetreu auf Prüfständen nachzustellen.
Qualitätssichernde Methoden wie Design- und Prozess – FMEAs und Softwareentwicklung nach Automotive SPICE sowie funktionale Sicherheitsanalysen nach ISO26262 begleiten die Entwicklungsprozesse bis zum Serienanlauf und darüber hinaus.
Wir bei SHW haben sämtliche notwendigen Kompetenzen zur Entwicklung komplexer mechatronischer Systeme, bestehend aus Mechanik, Hydraulik, Elektronik und Software, unter einem Dach vereint.
Von der Idee bis zum Serienprodukt werden unsere Systeme über alle Phasen des Produktentstehungsprozesses in unserem Entwicklungszentrum in Bad Schussenried konzipiert und konstruiert.
Parallel dazu entwickeln unsere Ingenieure elektronische Schaltungen und die dazugehörige Embedded Software Hand in Hand mit den hydraulischen Funktionalitäten.
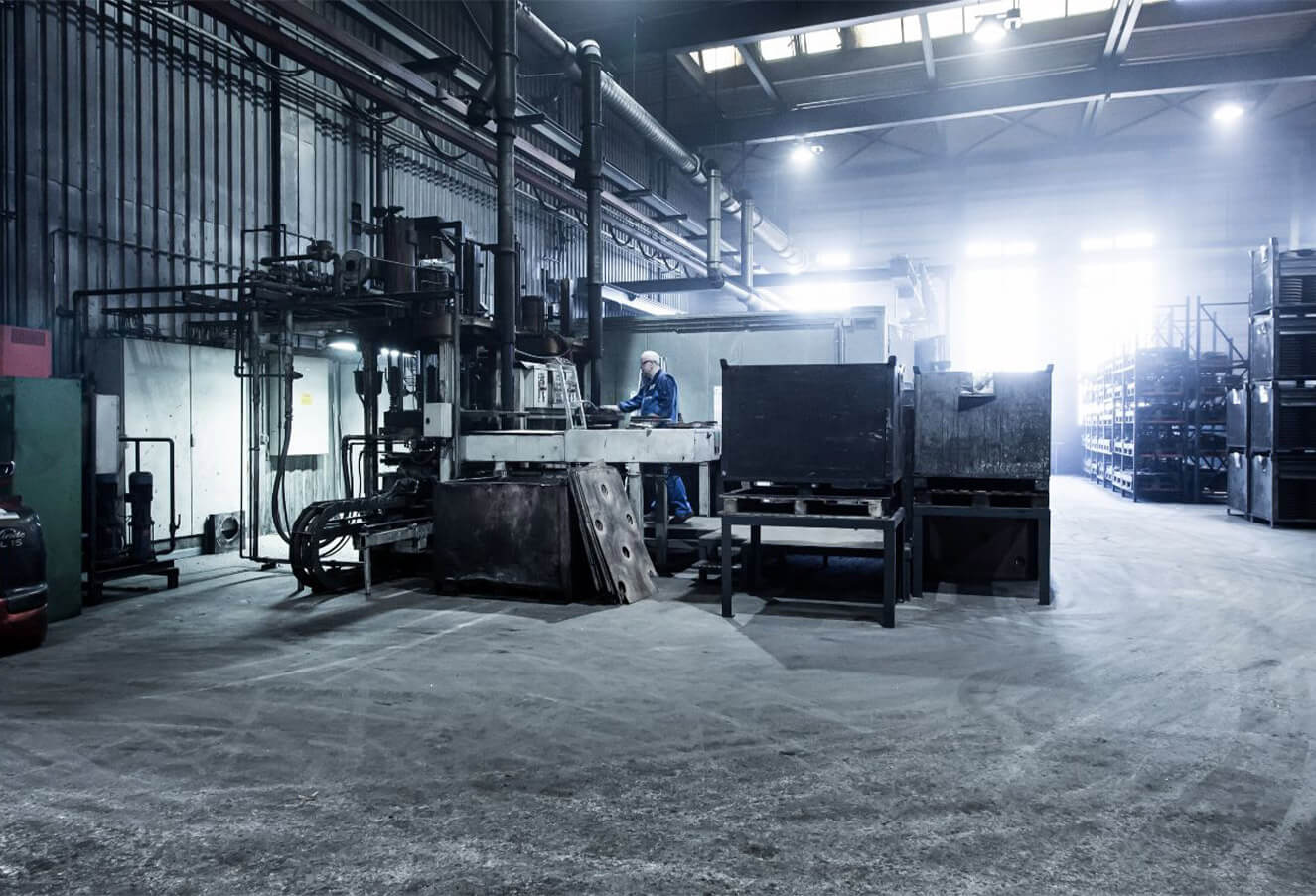
Effizienzverbesserung
Weiterhin entwickelt die SHW Präzisionsform- und Fügeprozesse für hochgenaue, hydraulische Bauteile, die in Ölpumpen und Nockenwellenverstellern verbaut werden und auf die Reduzierung von Leckagen abzielen. Um die CO2-Emissionen weiter zu reduzieren, werden zunehmend dünnere Motor- und Getriebeöle eingesetzt. Damit möglichst geringe Leckagen in hydraulischen Systemen auftreten, sind noch engere Spaltmaße erforderlich. Mit innovativen Umform- und Fügelösungen – beispielsweise Impulsrichtverfahren – entwickelt SHW hochpräzise Sinterbauteile für Motor- und Getriebeölpumpen sowie für Nockenwellenversteller und verbessert dadurch deren Energieeffizienz.
SHW erforscht und verbessert die lokale Oberflächenverdichtung für hochfeste Zahnräder und verschleißarme Kettenräder. Sinterteile sind von Haus aus zu einem gewissen Grad porös und zeigen deshalb im Vergleich zu konventionellem Stahl verminderte mechanische Eigenschaften.
Mit dem Verfahren der selektiven Oberflächenverdichtung in hochbeanspruchten Bauteilzonen werden mechanische Eigenschaften annähernd denen von Kompaktstahl erreicht. Damit kombinieren wir die besonderen, pulvermetallurgischen Formgebungsmöglichkeiten mit der hohen Leistungsfähigkeit von Stahl. Die Vorteile spielt die Oberflächenverdichtung vor allem bei hochfesten Zahnrädern und verschleißarmen Kettenrädern aus. Daraus entstehen verbrauchsreduzierende Systeme, die nur mit pulvermetallurgischen Komponenten wirtschaftlich umsetzbar sind.
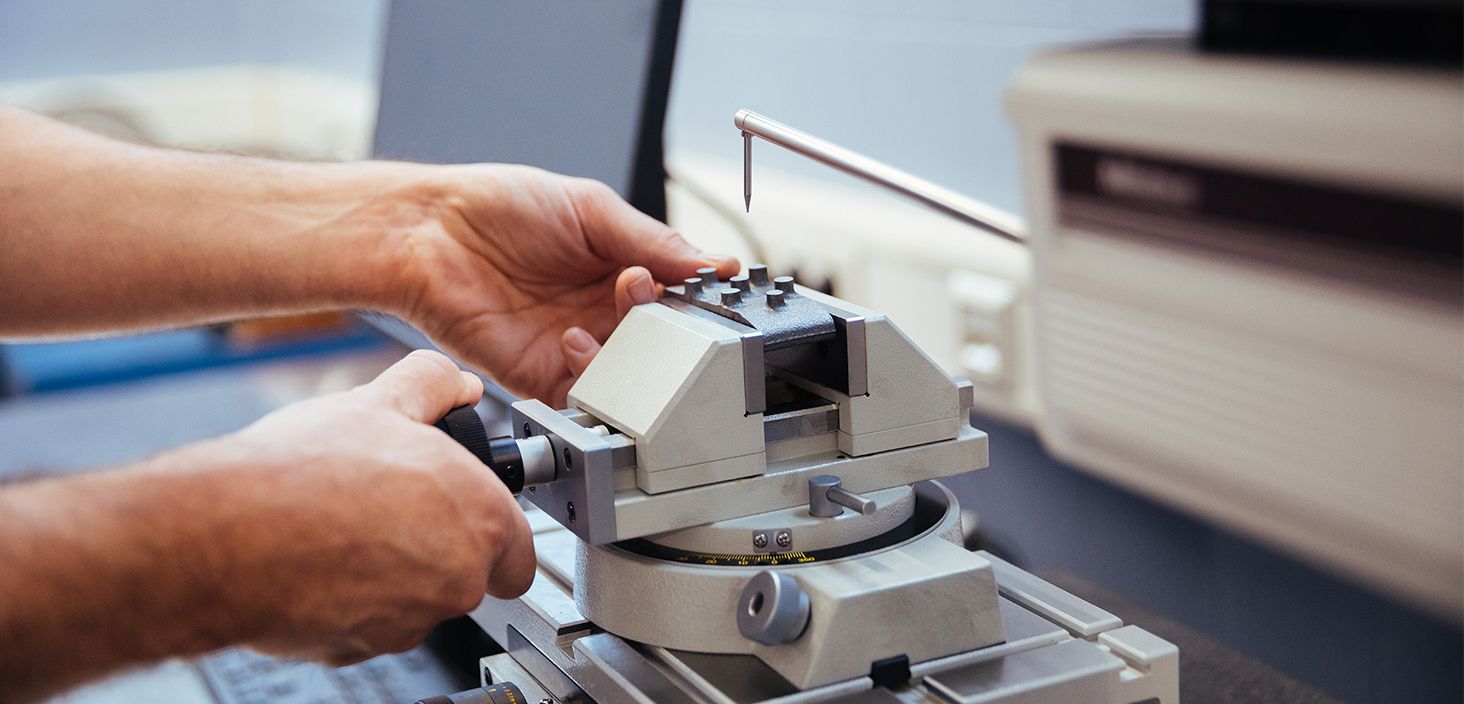
Meilenstein-Reviews
Während des Entwicklungsprozesses finden mehrere so genannte Meilenstein-Reviews statt. Hier werden Ergebnisse reflektiert und somit sichergestellt, dass die künftige Bremsscheibe die beidseitigen Anforderungen erfüllt. Erst wenn sämtliche Vorgaben eingehalten sind, wird die Konstruktion freigegeben.
Der Freigabe folgen Konzeption und Konstruktion der Gießwerkzeuge. Ihre Fertigung findet im SHW-eigenen Werkzeugbau statt. Unter Verwendung dieser bereits serienwerkzeugnahen Gießwerkzeuge werden erste Entwicklungsmuster gegossen und anschließend bearbeitet.
Damit die spätere Bremsscheibe alle festgelegten Funktionen erfüllt, wird sie anhand erster Entwicklungsmuster auf dem SHW-eigenen Bremsenprüfstand validiert. Dazu werden diverse Prüfungen gemäß kundenspezifischer Versuchsrichtlinien durchgeführt.
Erst wenn die Produktvalidierung auf dem Prüfstand erfolgreich bestanden ist, gehen Entwicklungsmuster an den jeweiligen Kunden. Dieser kann beispielsweise erste Versuche im Fahrzeug durchführen.
Mit der Entwicklungsabteilung des Kunden werden die Ergebnisse aus den Versuchen diskutiert und etwaige Verbesserungen des Produktes bis zu Serienreife beschlossen und umgesetzt. Erst dann wird die Bremsscheibe in Serie hergestellt.
Den Ausgangspunkt bildet das Lastenheft, das sämtliche Anforderungen an die Bremsscheibe festhält und die Basis für ihre Konzeption und Konstruktion bildet. Schon in der Entwicklungsphase stellen diverse Simulationen sicher, dass die Bremsscheibe alle relevanten Funktionen erfüllt. Das vermeidet Kosten und spart wertvolle Zeit. Simuliert wird beispielsweise, wie sich die Bremsscheibe bei einem Temperaturanstieg während des Bremsvorgangs verformt. Dies ist unter anderem für den Bremskomfort wichtig. Mit verschiedenen Entwicklungsmethoden, beispielsweise der so genannten Fehlermöglichkeits- und -einflussanalyse (FMEA), werden Risiken identifiziert und Gegenmaßnahmen getroffen.
Die jeweiligen Anforderungen an die Bremsscheibe müssen wirtschaftlich umsetzbar sein. Spezialisten aus der Produktion bewerten daher die Gieß- und Bearbeitbarkeit und schlagen mögliche Anpassungen vor, die zusammen mit dem Kunden beschlossen werden. Auch hier werden Simulationen eingesetzt. Beispielsweise wird der Gießprozess simuliert, um Erkenntnisse zur Herstellbarkeit und Qualität der Bremsscheibe zu erhalten.